Katalytische Gas-Flüssig-Reaktionen mit dem BUSS-Loop® Reactor, aber nicht nur…
BUSS ChemTech hat sich mit dem BUSS-Loop®-Reaktor, der erstmals in den 1950er Jahren für die Hydrierung von Fetten und Ölen verkauft wurde, einen Namen in der Verfahrens- und Reaktionstechnik gemacht. Seitdem haben wir das System kontinuierlich weiterentwickelt und das Know-how auf Nebenaggregate und Prozesse ausgeweitet.
Heute bieten wir eine breite Palette von Dienstleistungen rund um einen maßgeschneiderten industriellen BUSS-Loop® Reaktor an, der für den Batch- oder Semi-Batch-Betrieb oder für den kontinuierlichen Durchflussbetrieb mit einem integrierten Inline-Filtersystem ausgelegt werden kann.
Anlagen zur Vor- und Nachbehandlung, Katalysatoraufbereitung und -filtration, Mischen oder Trennen von Lösungsmitteln, Abtrennung von Nebenprodukten aus dem Reaktorkopfraum sind willkommene Herausforderungen, die unseren Verfahrens- und Projektingenieuren nicht unbekannt sind.
Wir können unsere Kunden bei einer Vielzahl von Gas-Flüssig-Reaktionen unterstützen. Einige von ihnen umfassen, sind aber nicht beschränkt auf:
- Hydrierungen (Bindungen aller Art)
- Alkoxylation
- Phosgenation
- Aminierung (auch reduktiv)
- Alkylierung (auch reduktiv)
- Chlorung
- Oxidation
- und viele andere…
Der Buss-Loop®-Reaktor
Die unübertroffene Lösung für hocheffiziente Reaktionstechnik
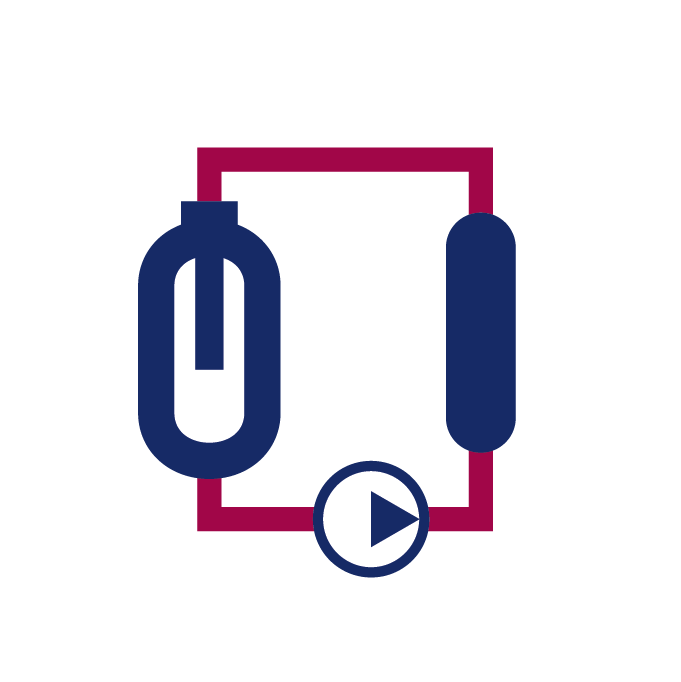
BUSS-Loop® Erläutert
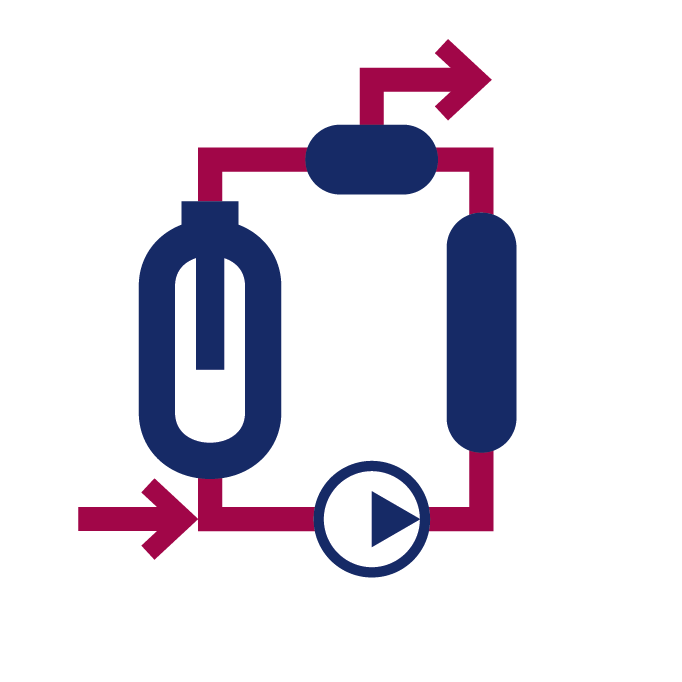
Kontinuierlicher Betrieb
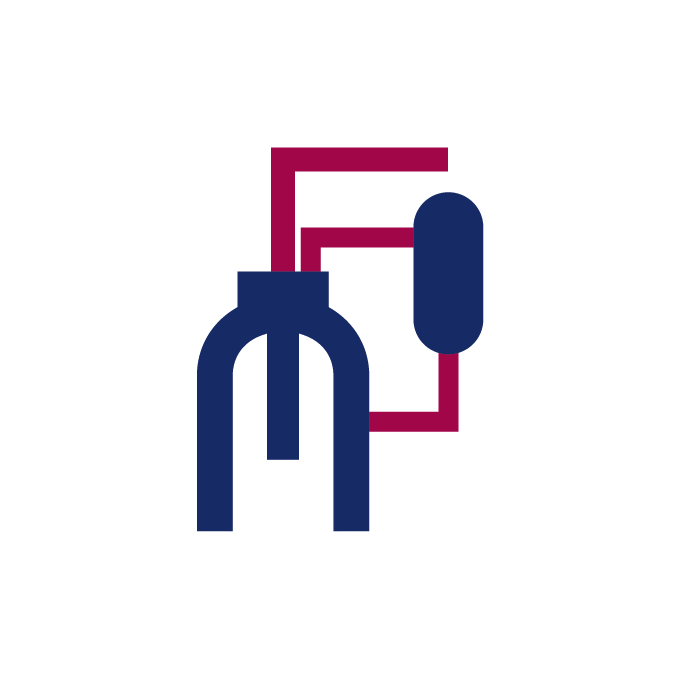
Der Gaskreislauf
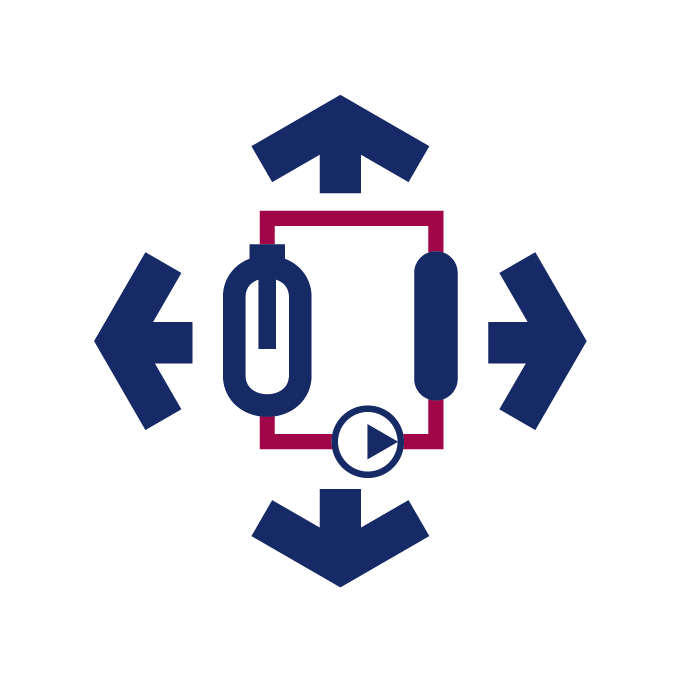
Die Skalierung des BUSS-Loop®
Ausgewählte Anwendungen des BUSS-Loop® Reaktors
[sp_easyaccordion id=“109268″]
TITEL
[sp_easyaccordion id=“109292″]
Erfolgsgeschichten
Kontaktiere uns
* Erforderliche Felder
Dein Kontakt
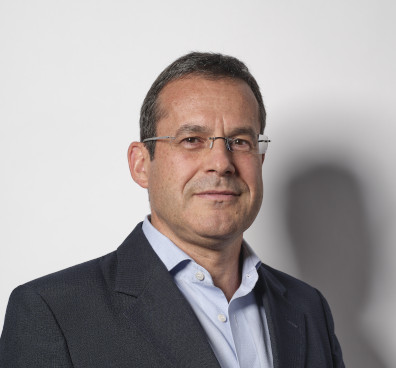
Gianluca Premoli
Business Manager Reaction Technology
Weitere Themen von Interesse
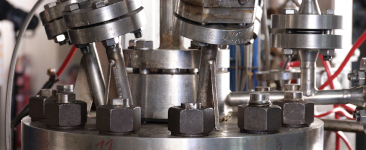
Unsere Entwicklungskapazitäten
Jede Anlage wird mit Garantien geliefert. Die Grundlage der Garantien sowie das Prozessdesign selbst werden in unserem eigenen umfangreichen technischen Zentrum entwickelt.
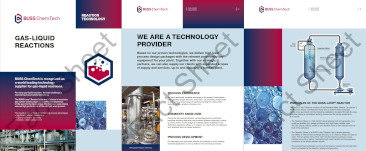
Merkblatt: Gas-Flüssigkeit-Reaktionen
Das Herzstück unserer Gas-Flüssig-Reaktionsverfahren ist die Technologie, die wir in den späten 1940er Jahren erfunden haben und die wir seitdem ständig verbessert haben.

Umfang der Projektlieferung
Von Technologiepaketen bis hin zu modularen und schlüsselfertigen Lösungen – klicken Sie unten, um sich über unser Dienstleistungsangebot zu informieren.